It’s been raining a lot lately, and that is great news for tyre developers testing the wet performance of their latest products. Not so good if they’re trying to test tyre performance in the dry, and it would be better to go indoors in search of better weather. Continental has done precisely this.
The manufacturer of the Continental, Uniroyal and Semperit tyre brands opened its Automated Indoor Braking Analyzer (AIBA) facility in 2012 for the purpose of conducting weather- and driver-independent braking tests at its main proving ground, the Contidrom. There’s plenty to see inside the AIBA hall when we visit in July, but as we pass through the main entrance, our host Philipp Must mentions the site’s no photography policy. As Continental’s Head of Technical Customer Interface Management Worldwide and the AIBA’s very first manager, he knows the rules, but my camera suddenly feels twice as heavy. I’ve never wanted to take a photo more than now.
In addition to an assortment of vehicles equipped with what look like over-engineered GoPro mounts at the front and locomotive couplings under the tailgate, what I’m itching to photograph is the 75-metre braking track and accompanying turntable. Philipp Must tells us that staff can adjust ambient temperatures in the hall from 10 to 25 degrees Celsius, while a hydraulic system effortlessly swaps in and out five different road surfaces for wet and dry testing.
Behind a closed door is a separate ice braking hall whose track temperature can vary between -10 and -1 degrees, with air temperatures ranging from 5 to 12 degrees. Unlike the wet and dry braking facility, the ice track relies on a human to do the braking.
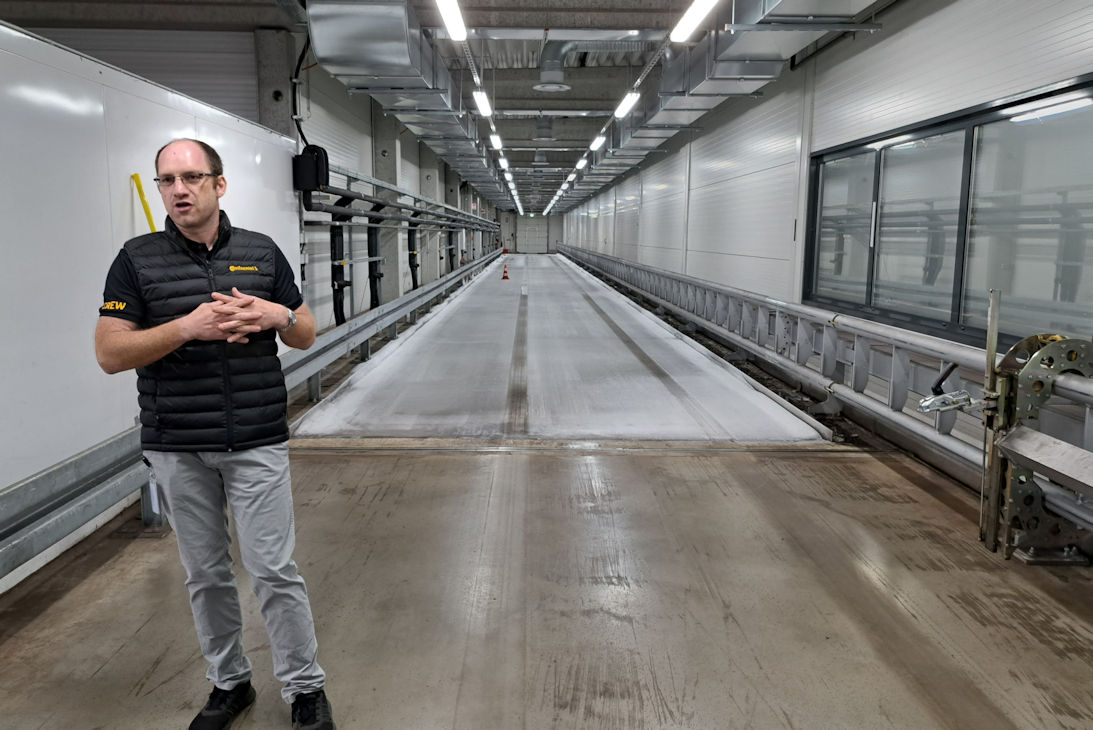
Philipp Must within the ice track, one of the few places within AIBA where photography is permitted (Photo: WhatTyre / Stephen Goodchild)
All the fun of the fair
Must draws our attention to the cars and SUVs that will be used in wet or dry testing later, each brimming with electronics and equipped with a robotic leg that presses the brake pedal. The coupling at the back is welded to the vehicle’s frame (forever ruining it for on-road use) and will connect it to a rail apparently inspired by hardware used in amusement parks. The front-mounted gadget turns out to be a laser sensor.
Describing AIBA’s technology to his uninitiated guests, Must says that “an electromagnetic accelerator on a rail-mounted sled pushes the car forwards with an equivalent of 1,000 horsepower, driving the vehicle forward like a funfair rollercoaster.” When a predetermined spot is reached on the track, the sensor at the front of the car picks up a signal that informs the brake robot it is time to push the pedal. “The robotic leg can brake with a force of 800 Newtons, the equivalent to a human leg performing an emergency braking manoeuvre that triggers the car’s ABS system.”
The electromagnetic accelerator can propel a vehicle to 115 km/h (71.5 mph) within 3.4 seconds. The corridor evaluation for brake testing is between 110 and 0 km/h in dry conditions and between 80 and 0 km/h when the AIBA’s waterworks are operating.
Precision is vital
The key advantages of facilities like AIBA are accuracy and repeatability. Standard practice at AIBA is to repeat each braking test seven times. The average difference in stopping distances for the seven wet tests we witnessed was 15 centimetres, as opposed to the 1.0 to 1.5 metre variation we may have encountered outdoors. Continental also claims that by automating braking and keeping out the weather it can enhance reproducibility by 70 per cent, and this improvement isn’t just nice to have.
“When we introduced silica into our tyres a couple of decades ago, we embedded new polymers into the compounds that shortened braking distances by a double-digit percentage. This was a major leap forward for our tyre developers,” comments Must. “Today we are searching for every single stone that we need to turn to find something that further shortens braking distance. This is why we need a measurement device precise enough to work with the small changes we achieve through material design and compound recipes.”
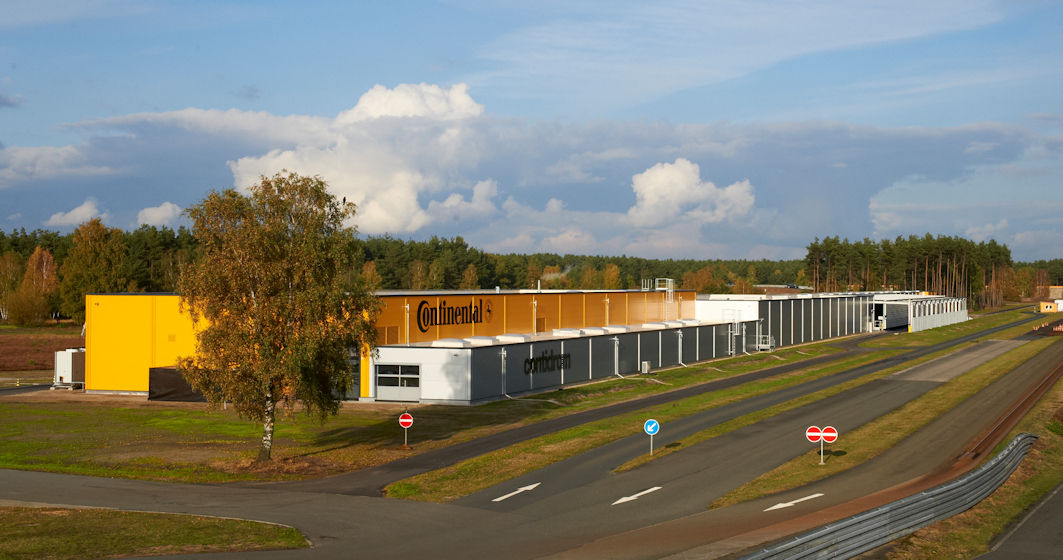
AIBA opened in 2012 for the purpose of conducting weather- and driver-independent braking tests (Photo: Continental)
In-depth analyses with AVA
In addition to modified cars and SUVs, in 2019 Continental began using a fully electric test vehicle for measuring car tyre braking performance. Called AVA – short for Analytic Vehicle AIBA – this vehicle differs from its car-based counterparts in that it can autonomously measure dynamic tyre characteristics on real roads. Testing with AVA not only results in brake distance measurements, but also determines and records the slip of the tyre, its longitudinal power transmission and the tyre load.
This test method provides Continental’s development team more in-depth analyses of dynamic tyre properties without influences from a specific vehicle. There are virtually no restrictions on rim or tyre size, and the load acting on each mounted wheel can be varied between 250 and 1000 kg. The AIBA team can thus set test conditions for small passenger cars through to vans. AVA is certified for wet braking testing according to the EU tyre label and in future will also be used for this purpose.
AVA won’t completely replace other test methods, as Philipp Must points out a significant benefit of using conventional cars and SUVs. “Our Automotive group sector develops ABS systems and sells these to OEMs. We benefit twice over when selecting a vehicle fitted with Continental’s MK C1 braking technology, for example, as we can sit together with our Automotive colleagues and conduct joint testing with their brake system developers. They appreciate the high precision gained when removing the weather influence and can learn how the ABS works with a certain set of tyres.”
Testing 16 hours a day
The AIBA team tests between 6am and 10pm, with two shifts looking after operations. Must is proud to tell us that AIBA is now responsible for more than 65 per cent of Continental’s passenger tyre brake testing. He’s reluctant to take us further behind the curtain and reveal how many tests take place each day, but according to Continental the facility can theoretically run up to 15 tests every hour.
After observing automated wet braking tests, it was time to visit the ice track. No tests were being carried out at the time and instead Philipp Must invited his guests to compare summer and winter tyre grip levels on icy surfaces by wearing flip-flops with soles made from actual tread patterns. Summer slippers proved wholly unsuited to the task and should be mandatory footwear for anyone who thinks cold weather tyres are never necessary.
Upon leaving AIBA, a main benefit of the facility immediately hit home once more. The Contidrom was silent save for the rustling of the trees beyond the perimeter fence. Strong winds had necessitated a pause in outdoor testing, but all was business as usual inside – where the AIBA test team had selected their own weather.